Symptom: Shorted magnet driver transistor
Location: Lyons, Colorado.
This is a case where a component failure revealed a design flaw that has been plaguing Addams Family pinball machines. There have been a lot of reported problems with the magnets under the center of the playfield that are energized in some modes like the seance mode.
(Note: the “too long; didn’t read” answer here is to remove D17 from the Power Driver board.)
On this particular machine, transistor Q1 on the magnet driver board which is mounted on the underside of the playfield, was shorted. This transistor powers the left magnet. I replaced transistor Q1 only to see smoke appearing a few minutes later. The transistor was very hot. The magnet checked out okay, with a resistance between 4 and 5 ohms. Upstream from Q1 is Q44 located on the Power Driver board. I tried replacing Q44, thinking that it wasn’t turning off all of the way. It didn’t help.
While checking on possible causes, I noticed that the solenoid power in the machine was only measuring about 47 volts. But the voltage to the magnets was about 70 volts (normal). This difference was abnormal since both power supplies have the same AC source. The oscilloscope revealed that capacitor C8 was bad on the Power Driver board. This capacitor filters the pulsating DC from the rectifier bridge (BR3). Although the schematics show the voltage as being 50 volts, it will measure 70 volts with no load (i.e. no solenoid powered on).
After replacing the capacitor, the Q1 transistor no longer got hot. I still needed to answer the question as to why it was getting hot in the first place, and why the other two transistors for the other magnets were not doing the same thing.
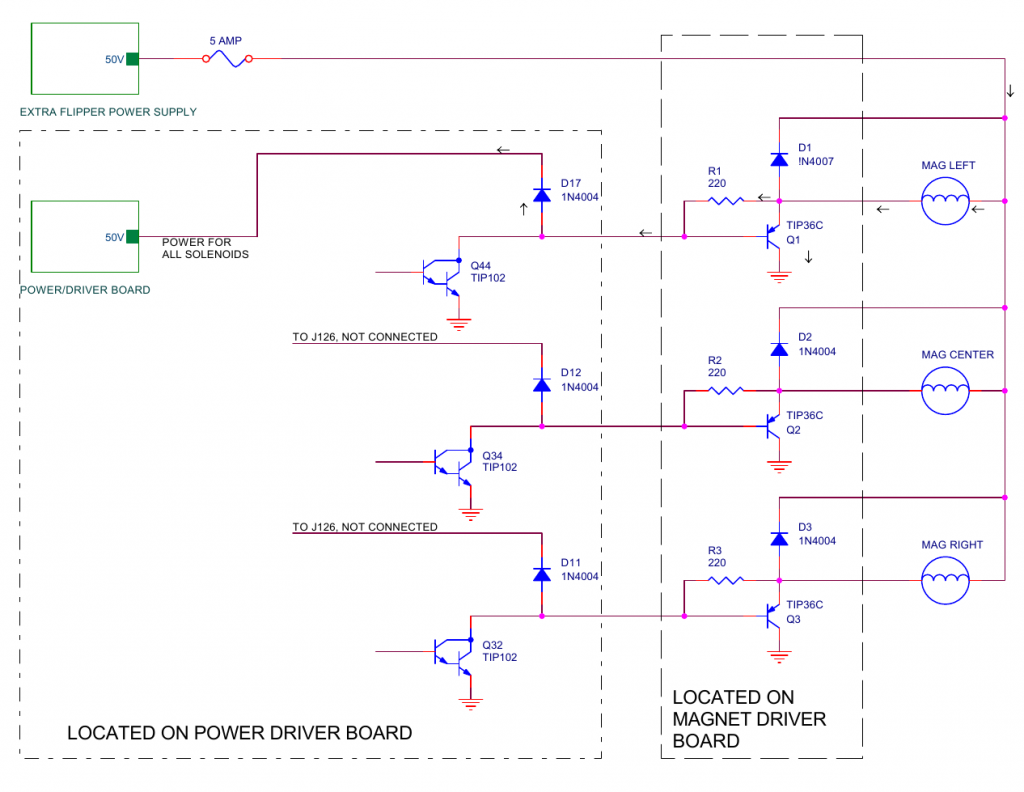
The schematics from the manual don’t show it, but the magnets are powered by the Extra Flipper Power Supply board, which also powers the upper flippers on the playfield. All other solenoids are powered by the Power Driver board.
With the failure of capacitor C8, the solenoid power supply had a lower average voltage than the flipper power supply. Following the arrows in the above diagram, the power supply with the higher voltage flowed through the magnet, through R1, and through D17 to the power supply with the lower voltage. As the current went through R1, a voltage drop developed across R1, which turned on transistor Q1, causing more current to flow to ground through the transistor, which turned on the magnet (at least partially). The magnet and the transistor are only designed to be turned on in short pulses, not continuously like in this case which causes overheating.
After the capacitor was replaced, the voltage on both power supplies was the same. The current was no longer flowing from one to the other, the transistor turned off, and there was no power going through the magnet. UNTIL…
When any of the solenoids fire such as a pop bumper, slingshot, or ball kicker, the voltage on that power supply will drop, thus momentarily turning on transistor Q1 again. On a heavily used machine, where there are a lot of multiballs, I believe that transistor Q1 overheats and eventually fails.
The other magnet driver transistors are not affected because diodes D11 and D12 are not connected to anything. Their cathodes connect and dead-end at connector J126. So only D17 is causing a problem. These tieback diodes are only used when the driver transistors are directly driving a solenoid coil. In this case, the driver transistors are driving another set of driver transistors (ones that can handle the increased power of the magnets). So these diodes are superfluous. The actual tieback diodes for the magnets are on the magnet driver board (see D1, D2, and D3 in the schematic above).
The solution is to remove D17, which is simple enough to just cut one end of it with a wire cutters. Once the diode is cut, the Power Driver board can’t be used in a different titled machine without reinstating the diode. The Power Driver board is used in many Williams pinball machines from the era and is not customized for each game title.