Auctions
If you’re looking for a used pinball machine, stay away from auctions. I have a number of customers who have purchased machines through various arcade related auctions that were in substantially below average condition. Perhaps the customers who get good machines from auctions don’t contact me which gives me a biased view. But the machines I have worked on that came from auctions have been atrocious (especially one with Captain in their name). Usually it’s a case of missing parts or bypassed functions so that the machine appears to be working but actually isn’t.
After-market Boards
It is usually much better to have an original circuit board repaired than it is to buy an after-market replacement. People wrongly think that if it’s new it must be better. But as more people repair their own pinball machines, the easiest thing to do is to buy replacement boards.
Over the years I’ve had a number of problems with Rottendog boards. They might be gradually improving, but I’ve had one problem after another with them. Here’s just a recent example. I recently purchased a new CPU/sound board (MPUWS) for a Sega, Lost World Jurassic Park pinball machine. Compared to the original board, a section of circuitry was omitted from the design presumably to save on cost. Needless to say, the board didn’t work in the machine. None of the optical sensors worked.
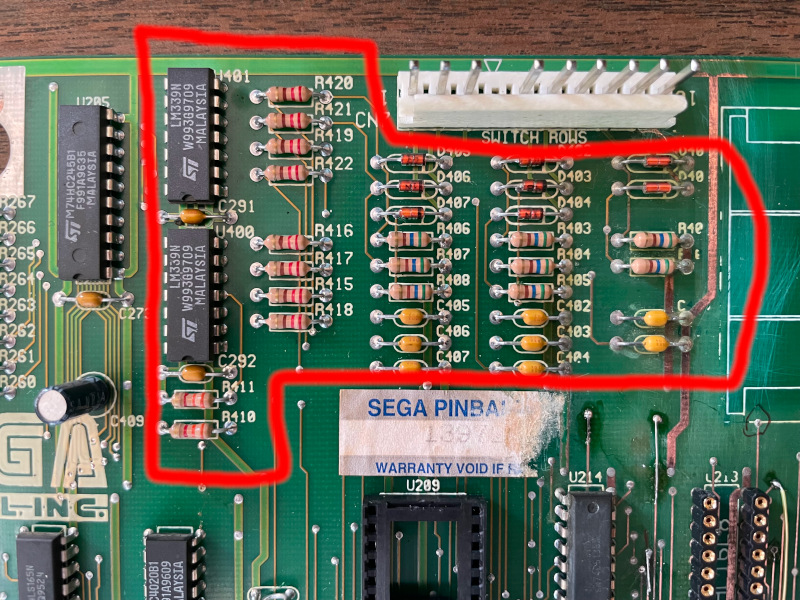
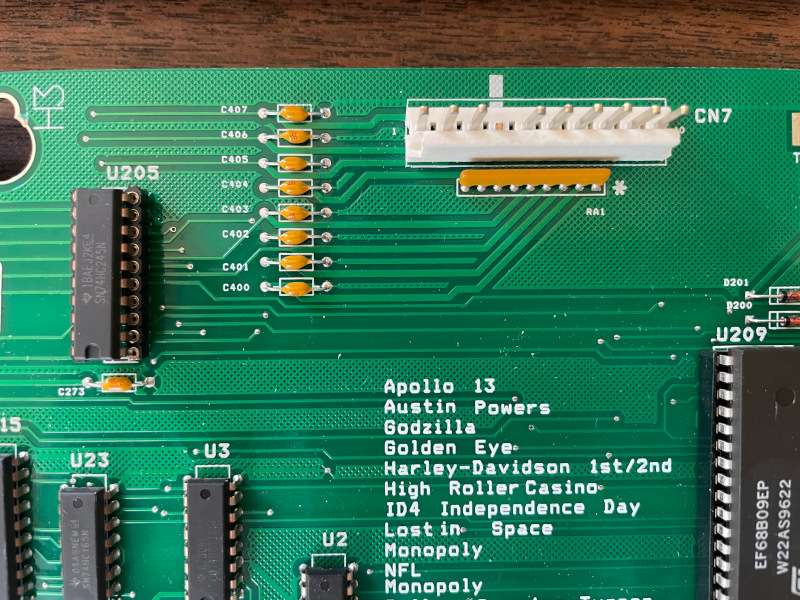
The original board was suffering from substantial battery corrosion. In the end, I ended up removing the corrosion and repairing about a dozen traces on the original board and using it instead of the Rottendog board.
Another manufacturer is X-pin. I recently worked on a Back to the Future pinball machine made by Data East. The owner had an X-pin PPB board installed. The board had shorted transistor on it. This is a really common problem in pinball machines. X-pin chose to use surface mount transistors that are not field repairable.
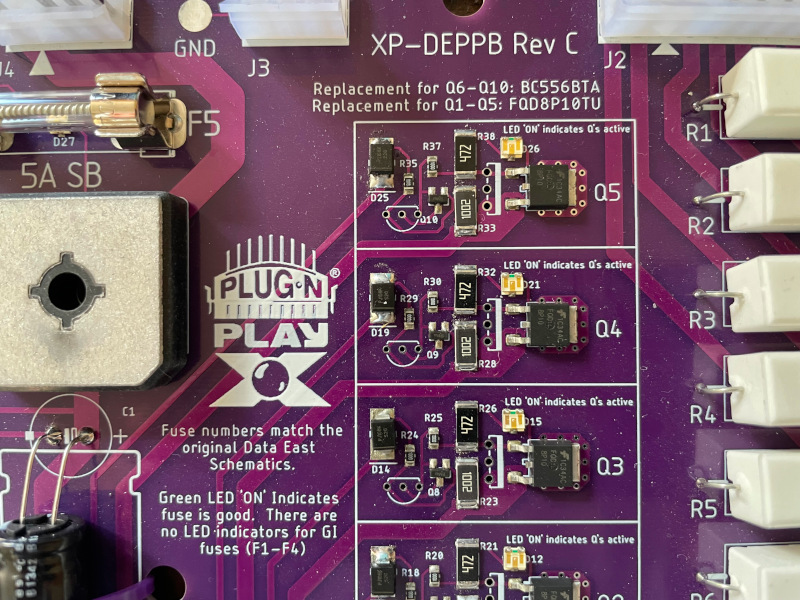
I have the special equipment to repair surface mount parts, but it’s not something I can drag with me to a customer’s home. Every pinball manufacturer uses through-hole technology in their solenoid driver circuits. Through-hole parts can easily be replaced in the field and by anyone who has decent soldering skills. The only reason X-Pin chose to go with surface mount is to save on assembly cost. I’m a former electronics engineer and have decades of experience with this.
Fortunately in this case, the owner of the pinball machine still had the original PPB board. I was able to get that up and running on the spot. I only brought back the X-pin board to my office so the owner could have a backup.
There are a few aftermarket board manufacturers that I have good experiences with. One is Alltek. They supply boards for the early solid state Bally and Stern machines. I’ve probably installed over 50 of their boards and never had a problem. Another manufacturer I haven’t had issues with is Ni-Wumpf who make boards primarily for Gottlieb pinball machines. Another is Flippp, which is a non-profit located in France which charges a little more, but they are great circuit boards. There are other manufacturers out there who provide true to original designs.
I come to my repair appointments ready to repair common problems with original boards. I don’t stock parts for the after-market boards unless they are using the same parts as the original. I don’t like it when after-market boards stand in the way of a successful repair. I only recommend using them as a last resort.